Petrochemical
Mechanical Seals for Petrochemical Industry
Petrochemical
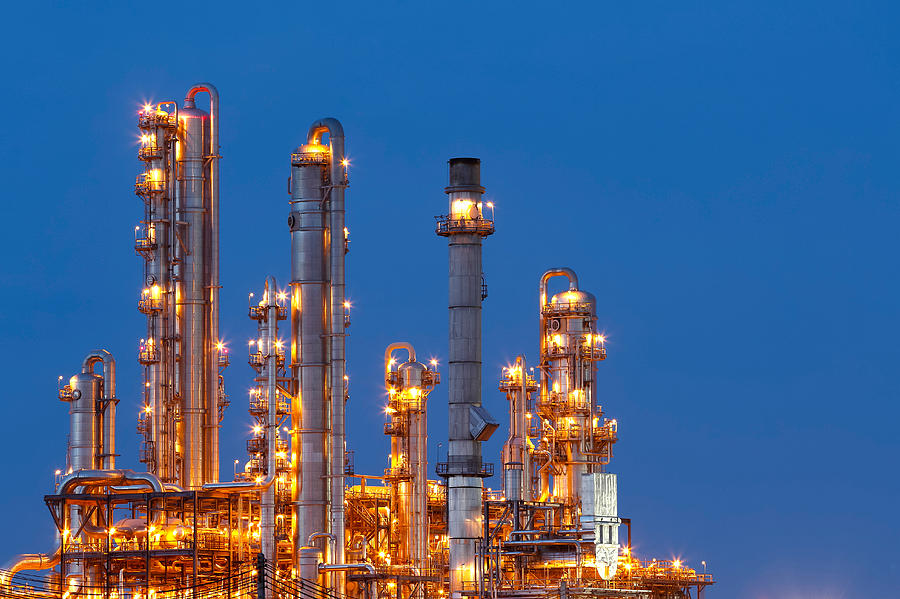
Mechanical Seals for Petrochemical Industry
Mechanical seals play a critical role in the petrochemical industry by preventing leakage of hazardous fluids and gases
Mechanical seals play a critical role in the petrochemical industry by preventing leakage of hazardous fluids and gases from pumps, compressors, and other rotating equipment. These seals are designed to withstand high pressures, temperatures, and corrosive environments commonly found in petrochemical plants. Here are some key considerations and features of mechanical seals used in the petrochemical industry:
- Material Selection: Mechanical seals for the petrochemical industry are typically made from corrosion-resistant materials such as stainless steel, Hastelloy, Inconel, or other alloys that can withstand the harsh chemicals and high temperatures encountered in petrochemical processes.
- Seal Design: The design of mechanical seals for petrochemical applications often involves robust construction with multiple sealing points to ensure reliable performance. This may include features such as dual seals, tandem seals, or cartridge seals, depending on the specific application requirements.
- Sealing Faces: The sealing faces of mechanical seals are critical for maintaining a tight seal. Materials such as silicon carbide, tungsten carbide, or ceramic are commonly used for the sealing faces due to their hardness, wear resistance, and compatibility with a wide range of process fluids.
- Pressure and Temperature Ratings: Petrochemical processes often operate at high pressures and temperatures, so mechanical seals must be rated to withstand these conditions without compromising their integrity or performance.
- Chemical Compatibility: Mechanical seals must be compatible with the various chemicals and solvents used in petrochemical processes to prevent degradation or failure due to chemical attack.
- API Standards: Many mechanical seals used in the petrochemical industry are designed and manufactured in accordance with standards set by the American Petroleum Institute (API), such as API 682, which provides guidelines for seal selection, design, and performance.
- Environmental Regulations: Petrochemical plants must comply with strict environmental regulations, so mechanical seals should be designed to minimize emissions of volatile organic compounds (VOCs) and other pollutants.
- Reliability and Maintenance: Reliability is paramount in petrochemical operations, so mechanical seals should be designed for easy installation, inspection, and maintenance to minimize downtime and maximize equipment uptime.
- Safety Features: Mechanical seals may incorporate safety features such as seal support systems, leak detection systems, or pressure relief valves to prevent catastrophic failures and protect personnel and the environment.
- Customization: Mechanical seals for petrochemical applications are often customized to meet specific requirements such as shaft sizes, operating conditions, and industry standards.
Overall, mechanical seals are critical components in the petrochemical industry, ensuring the safe and efficient operation of pumps, compressors, and other rotating equipment in harsh and demanding environments.
The transport medium of rotating equipment is usually high temperature, high pressure, and flammable, explosive, toxic and fluid, and its reliability is particularly important. We at Sealomech engineering analyze Design and manufacture the seal structure, material and choose the suitable petrochemical mechanical seal for the pump,