Oil & Gas
Mechanical Seals for Oil and Gas Industry
Mechanical Seals for Oil & Gas
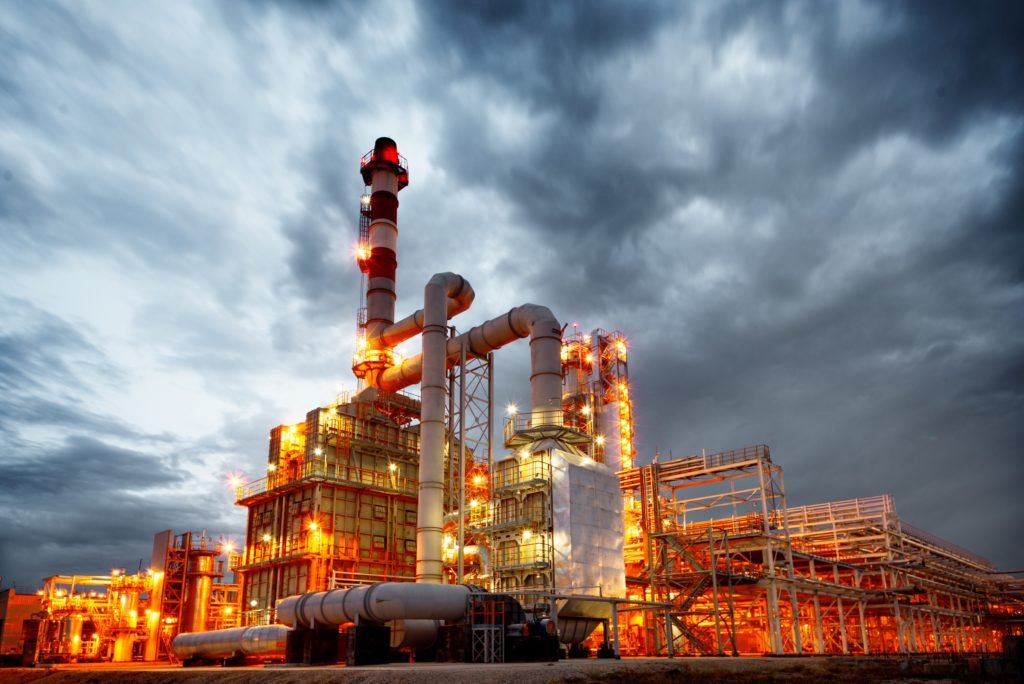
Mechanical Seals for Oil and Gas Industry
Mechanical seals plays important role to prevent leakage of fluids and maintain the integrity of critical components
Mechanical seals play a crucial role in the oil and gas industry, where they are used in various equipment and systems to prevent leakage of fluids and maintain the integrity of critical components. Here's how mechanical seals are utilized in the oil and gas sector:
- Pumps and Compressors: Mechanical seals are extensively used in centrifugal pumps, reciprocating pumps, and compressors deployed in upstream, midstream, and downstream operations of the oil and gas industry. These seals ensure the reliability and efficiency of fluid transfer and compression processes by preventing leakage of hydrocarbons, chemicals, and other fluids.
- Wellhead Equipment: Mechanical seals are employed in wellhead equipment, including casing heads, tubing heads, and Christmas trees, to prevent the escape of oil, natural gas, and other fluids from wellbores. These seals help maintain well integrity and prevent environmental contamination, contributing to safe and efficient oil and gas production operations.
- Valves and Actuators: Mechanical seals are integrated into various types of valves and actuators used in pipelines, refineries, and petrochemical plants. These seals provide tight shut-off and leakage prevention, ensuring the safe and reliable operation of process control systems in the oil and gas industry.
- Rotating Equipment: Mechanical seals are critical components in rotating equipment such as rotary pumps, mixers, and agitators used in refining and petrochemical processes. These seals prevent leakage of hazardous fluids and maintain equipment reliability, minimizing downtime and ensuring operational safety.
- Subsea Equipment: In offshore oil and gas production operations, mechanical seals are utilized in subsea equipment such as subsea pumps, valves, and connectors. These seals withstand high pressures, corrosive seawater, and harsh environmental conditions, ensuring the integrity and performance of subsea production systems.
When selecting mechanical seals for oil and gas applications, several factors must be considered, including:
- Material Compatibility: Seals must be compatible with the fluids, temperatures, and pressures encountered in oil and gas operations, including hydrocarbons, corrosive chemicals, and high-pressure gases.
- Pressure and Temperature Resistance: Seals must withstand the extreme pressures and temperatures present in oil and gas production, transportation, and processing systems without compromising sealing performance.
- Reliability and Longevity: Given the critical nature of oil and gas operations, seals must be highly reliable and durable to withstand prolonged exposure to harsh operating conditions and maintain sealing integrity over extended periods.
- Regulatory Compliance: Seals used in the oil and gas industry must meet regulatory standards and industry specifications for safety, environmental protection, and reliability.
Manufacturers of mechanical seals for the oil and gas industry typically offer specialized products designed to meet the demanding requirements of upstream, midstream, and downstream operations. These seals undergo rigorous testing and certification to ensure they meet the performance standards and regulatory requirements applicable to the oil and gas sector, contributing to the safety, reliability, and efficiency of oil and gas production, transportation, and processing activities.
Uncertain oil prices have increased the economic pressure on almost every asset and equipment maintenance and servicing. Fortunately, there are now extremely reliable and assured quality alternatives for high duty engineered mechanical seals
Post the rapid development in the oil and gas industry, Sealomech Engineering has made certain progress in the scale and technical level of their equipment. The mechanical oil and gas seal (Dry gas Mechanical seal and Wet gas Mechanical seal) also has become one of the most important research topics.These seals are almost always high-value assemblies. As an alternative to automatic replacement, repair technology now makes it possible to guarantee that future performance will be as good as that of a ‘new seal’
What makes Sealomech Engineering unique, is that we offer you a wide access to any brand expertise in the Oil & Gas sector, in turn assisting your organization dependence on seal manufacturers. Sealomech Engineering also offers service of mechanical seals for a array of applications majorly include, Main oil line (MOL) and booster pumps, Seawater injection pumps, Crude export pumps, NGL recycle pumps, Condensate pumps, Compressors and Power turbines.
Email Us: info@sealomech.com or Call Us: +91-8898230000